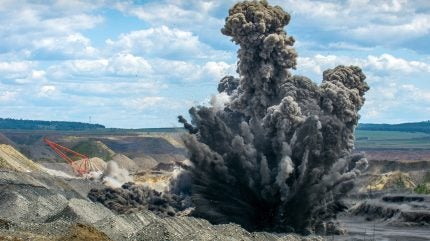
Automation in the mining industry has been burgeoning since the noughties, after the first successful commercial deployment of automated technology in open-pit mine haul trucks in 2007. Since then, it has proliferated to other mining equipment and both open-pit and underground mines.
Along with haul trucks, which are arguably the most automated of mining equipment today, autonomy in drilling equipment is now standard – ranging from remote control, tele-remote and semi-autonomous to autonomous – depending on a site’s requirements.
Analysis from PricewaterhouseCoopers shows the deployment of automated drills (considering varying levels of automation) in open-pit mines has grown at a compound annual growth rate of 74% since 2008. Furthermore, the adoption of automation and autonomous systems in drilling worldwide is one of the key drivers fuelling market demand for mining equipment.
“There is now an expectation that new drills from original equipment manufacturers [OEMs] will come automation-ready or capable,” says Wes Taylor, product manager for automation at Komatsu, a Japanese-headquartered manufacturer of mining equipment.
Mining majors see the benefit of investing in autonomous drilling
Drilling and blasting is one of the most dangerous mining processes undertaken. Degrees of automation enable drill rigs to do much of their work independently, effectively removing people completely, or lessening workers’ exposure to hazards such as dust, noise, vibration and, crucially, explosives. In countries where labour is expensive, this has the added side benefit of also reducing costs.
Another win from drill automation is improved productivity. “Operational consistency is one of the biggest key performance indicators for automation in drilling,” says Taylor. “Time to navigate to a hole, transition times and ability to hit the accurate hole and depth target are key factors that an automated drill can provide.”
How well do you really know your competitors?
Access the most comprehensive Company Profiles on the market, powered by GlobalData. Save hours of research. Gain competitive edge.
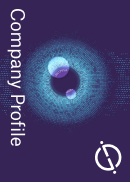
Thank you!
Your download email will arrive shortly
Not ready to buy yet? Download a free sample
We are confident about the unique quality of our Company Profiles. However, we want you to make the most beneficial decision for your business, so we offer a free sample that you can download by submitting the below form
By GlobalDataThis is why major miners have already invested heavily in the technology. Rio Tinto operates the largest autonomous drilling fleet in the world. It has 26 drill blast holes controlled from a remote operations centre where an operator can plan activities for each drill for an entire shift remotely, rather than doing the work manually on site.
AngloGold Ashanti rolled out a $6m (R111.62m) autonomous drill fleet at its Tropicana gold mine in Australia in 2020. The company said safety was a key factor in the decision, but as the equipment can operate throughout lightning and inclement weather and explosive detonation, and does not require fatigue breaks like employees, the technology had also improved operational efficiency and asset utilisation.
OEMs look to data and AI to optimise autonomous drilling technology
Komatsu’s base drill control systems found in its 320XPC, ZR77 and ZR122 blast drill models already contain automated capabilities such as Auto Drill, Auto Level and Auto Mast Angle (a ZR-specific feature) applications that support tele-remote operations. For full automation, the company offers an Auto Pilot system, an upgrade capable of completing an operational drilling mission previously defined by the operator.
Komatsu, along with other OEMs, is looking to optimise this process further by taking insights from data.
“Operators of drills, with their years of experience, can react to and adapt to the changing conditions of the mine and the drill,” says Taylor. “For automation of the drilling function, these events and the learned responses of operators are opportunities to improve the capabilities of autonomous drills to handle exceptions and properly manage the drilling function when the environment or conditions change.”
The company is working towards translating these learnings into its drill automation offering, including its pattern design and blasting requirements.
“With automation, there will be the ability to optimise and react to the changing conditions in the mine much faster as the machine will be capable of receiving updated missions and manage those changes without disrupting overall productivity or accuracy,” Taylor adds.
Jonas Albertson, chief technology operator at Swedish mining equipment manufacturer Epiroc, who has worked with the company for 25 years, agrees that data and AI are becoming more integral to improving drilling operations.
“Our customers have very complex operations and digital solutions that can support their decision-making and planning is important for them to keep their production plans on track,” he says. “A typical mine will have between 50 and 100 data sources, and we have built solutions where we can connect these and put them into our systems to aid real-time decision-making,”
Data-driven insights can be used to optimise the rock fragmentation after blasting to reduce the need for secondary demolition and create efficiencies in material handling.
These data-driven insights can be used to optimise the rock fragmentation after blasting, reduce the need for secondary demolition and create efficiencies in the material handling and the logistics of the mine, Albertson explains.
“In addition, miners are always trying to optimise the grades they extract, so grade control is another important element,” he adds. “How is the mineral or metal moving in the rock in the mine? How is the drill plan then being developed? Can you follow the rock after the blasting? Where is the hydrate and where is the low grade? There are a lot of different technologies involved.”
Epiroc’s AutoDrill and Rig Control System provide autonomous capabilities to its surface Pit Viper drills and other models. A fleet of the Pit Vipers is used at Boliden’s Atik mine in Sweden on a remotely controlled basis. The technology is also used by Rio Tinto in the Pilbara.
More recently, adoption of the technology is also being driven by sustainability, with more solutions becoming electrified as well as autonomous, says Albertson. In January, Epiroc launched three all-electric versions of Pit Viper models, meaning it has now electrified its complete Pit Viper line-up.
Advances in blasting
While automation in drilling has advanced apace, achieving the same in the blasting process is more challenging. This is largely due to the high variability between operations and difficult bench – where the explosion occurs – access, says Nigel Pereira, vice-president of new technology commercialisation at commercial explosives at blasting company Orica.
He says automation is expected to play a key role in helping miners get safe access to challenging orebodies due to the increasing demand for critical minerals.
Orica’s Avatel technology for underground mining, developed in partnership with Epiroc, hopes to address this problem by automating all aspects of the explosives-handling process for underground blasting and removing people from the process altogether.
Automation is expected to play a key role in helping miners get safe access to challenging orebodies due to the increasing demand for critical minerals.
The technology, which the company says is a first-of-its-kind innovation, enables a single operator to prepare the development face and charge explosives from the safety of an enclosed cabin several metres away. The system can access drilled holes by dewatering and cleaning the face, then efficiently locate, measure, flush out, prime and load the blast holes.
In addition, Orica says its WebGen system, a fully wireless electronic explosion initiation solution, removes the need for workers to return to the face after loading to detonate the explosives, improving safety and streamlining the blasting process.
This has, Pereira added, helped reshape mining schedules to reduce downtime and boosted turnaround and stope ore recovery rates.
ABB, meanwhile, has developed what it calls the ABB Robot Charger which can detect drilled holes in a rock face and install explosive charges during mining operations, removing the need for human presence. The application was successfully tested in October 2023 at a Boliden mine.
The path to fully automated blasting
Pereira says blasting is one of the few remaining processes to develop fully automated systems, but the industry is advocating for this transition, even if there are still challenges related to cost and productivity that will likely persist, mirroring past experiences with other automated mining practices.
“Initially, we see the industry adopting automation to remove people away from the most hazardous areas of mining, with subsequent attention shifting towards leveraging technology to revolutionise mining practices, ultimately reducing operational expenses and boosting productivity,” he says.
“We are seeing this with Avatel in developmental blasting, where despite the higher costs associated with face blasting, significant cost efficiencies and productivity gains can be achieved by eliminating the need for ground support at the face traditionally used to protect personnel during charging.”
Similarly, although far more advanced, drilling automation faces its own challenges, one being the overall perception and understanding of what is needed to add automation into drilling process, says Taylor. This is something OEMs must look to address.
“The technology is moving extremely fast and can be viewed as a ‘black box’ which drives at some hesitation to integrate and support automation,” he says. “For Komatsu, our goal is to focus on providing proper training, documentation, service and support with change management to help break down this barrier, so customers understand that automating equipment does not always require a massive change to the mines process, infrastructure and skill sets.”