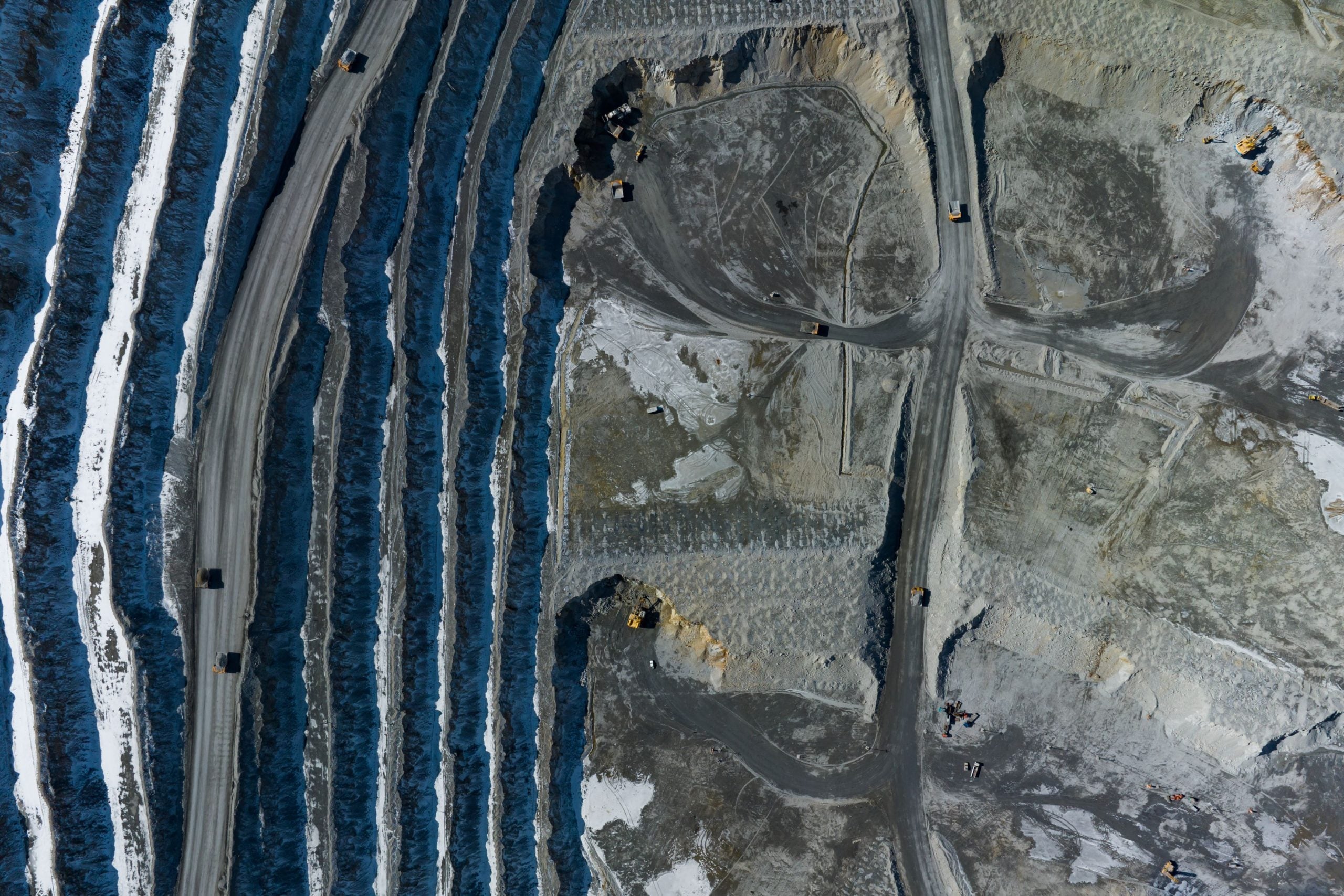
The vast quantity of technology, tools and machinery needed to operate a modern mine makes for huge business, and this is reflected in the ballooning value of the mining industry and its adjacent sectors. According to Allied Analytics, the global mining equipment market set to be worth $182bn by the year 2030, and the world’s industries are showing few signs of lowering their appetite for raw minerals. Demand for iron ore alone is set to increase by a combined annual growth rate of over 4% between 2022 and 2026.
To meet this growing demand, mining companies themselves, and technology firms with an interest in the mineral sector, are constantly bringing new products to the market. Technological advances are happening every day, especially in a sector such as mining where automation and remote operation are commonplace, and these new processes are being implemented at a pace and on a scale never seen before.
From technological buzzwords in drones and AI to new uses for humble vegetable oil, the equipment used in the mining industry is undergoing a sudden and striking change. With more pressure on miners than ever to deliver minerals efficiently and cost-effectively, while minimising their environmental footprints, mining equipment could make a real difference in the sector’s future.
Drones and precise mapping
Using drones to map mines both above and below ground is nothing new, with autonomous drones being flown into Australian gold mines as early as 2017. But Flyability’s new Elios 3 drone goes even further in adapting to the unique challenges of operating drones in the most testing of environments.
With both 4K and thermal cameras on board, LIDAR (Light Detection and Ranging) laser mapping systems and a lighting system capable of delivering 16,000 lumen with special “dust safe” modes, it’s capable of capturing data and mapping mines previously thought to be entirely inaccessible. It’s strong and flexible too, with a carbon fibre protection cage shielding the device from collisions.
The combination of thermal cameras, LiDAR laser distance mapping, and the 4K video allows the drone to produce a 3D ‘live map’ of a mine accurate to the centimetre, even without GPS. Flyability reports that these maps are already being used by inspectors to see the precise location of defects, even when high dust levels make camera feeds difficult to see.
How well do you really know your competitors?
Access the most comprehensive Company Profiles on the market, powered by GlobalData. Save hours of research. Gain competitive edge.
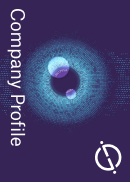
Thank you!
Your download email will arrive shortly
Not ready to buy yet? Download a free sample
We are confident about the unique quality of our Company Profiles. However, we want you to make the most beneficial decision for your business, so we offer a free sample that you can download by submitting the below form
By GlobalDataIt’s proven itself to be a huge asset, with operators at one Colorado mine using the Elios 3 to locate an ore pass hangup in a mere ten minutes, having spent two months failing to locate and clear the blockage manually.
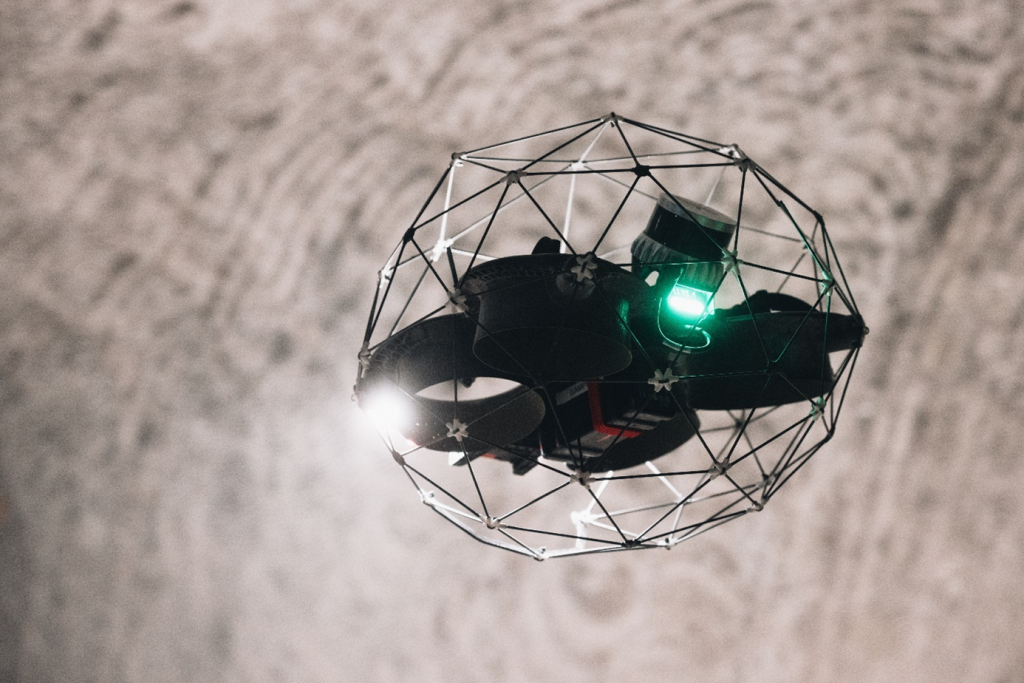
Vegetable oil used to decarbonise equipment
The mining industry has been grappling with decarbonisation for some time now, and the pressure to hit net-zero targets is greater than ever. But one major leap forward for emission reductions may come from an unlikely source: vegetable oil.
In February, BHP announced that it would be trialling the use of Hydrotreated Vegetable Oil (HVO) to power mining equipment at its Yandi Iron Ore operations in Western Australia, thanks to a collaboration with BP.
HVO is a diesel-like fuel made by breaking down large molecules found in vegetable oils. Most diesel engines can run HVO and similar fuels with no modifications, and BHP plans to trial this renewable diesel in its haul trucks and other mining equipment over a three-month period.
According to BHP, approximately 40% of its operational greenhouse gas emissions came from diesel-powered equipment in 2020. With HVO fuel offering an up to 90% reduction in carbon dioxide emissions compared to regular diesel, this could mean a major step closer to a low-carbon mining industry.
BHP Western Australia iron ore asset president, Brandon Craig, sees the trial as a part of the net-zero transition.
“Ultimately, our aim is to have fully electric trucking fleets at our sites, but alternative fuels like HVO may help us reduce our emissions in the meantime while the electrification transition takes place.
“This collaboration with the teams at Yandi and bp is really exciting to see, given the potential application in our [Western Australia iron ore] business and BHP’s operations globally.”
Remote mining technology improves potash extraction
Following a series of near misses, serious injuries and fatalities across the global potash mining community, one company has decided to implement new technology to keep their operators safe.
Nutrien, which mines potash for the agriculture industry at six sites in Canada’s Saskatchewan province, recently used new remote mining technology to successfully mine a production wing without a single person entering the area.
In February, operators at Nutrien’s Lanigan potash site put the new remote system into action, and their success marks the first time in the company’s half-century of operations where a wing has been cut with no-one present.
Radar, LIDAR, high definition cameras that withstand dust and brand new advanced instruments for precision operations allow miners to retrieve material from a safe distance, avoiding damaging noise and dust exposure, as well as improving working conditions and ergonomics overall.
According to Nutrien, one unexpected benefit of the new system is an increase in productivity and operational processes, as the remote tech makes seamless transitions between operators during break and shift changes, allowing for mining to continually operate.
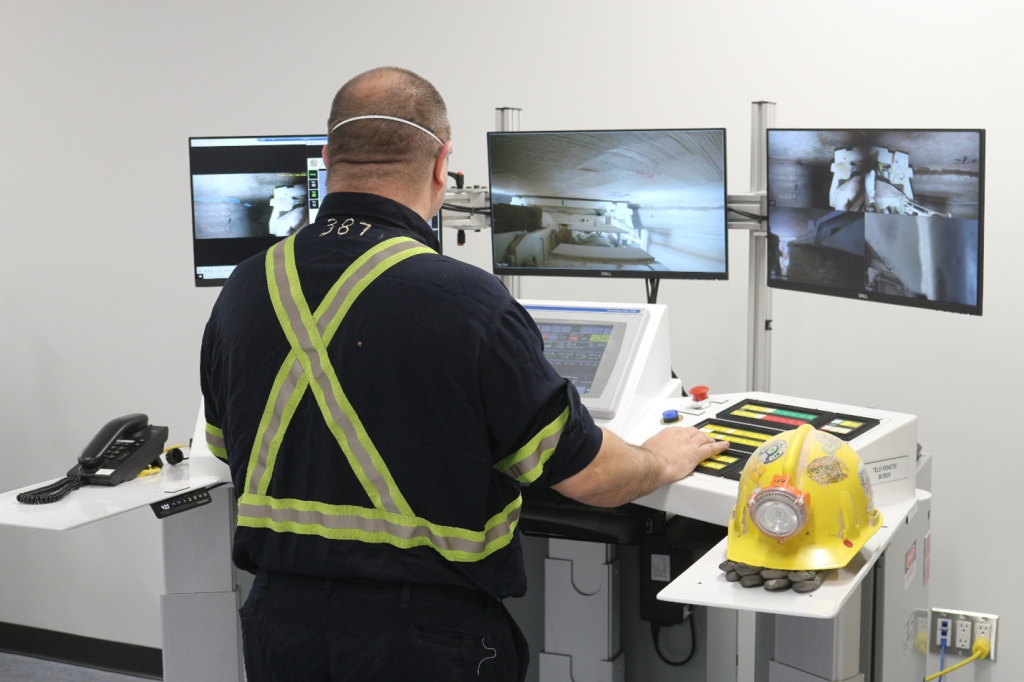
Trevor Berg, senior vice president of potash operations, sees this as a major step forward for the safety of potash miners. “This advancement significantly improves the safety of the operators by reducing exposures, while increasing overall productivity. This is a safety success story where we have truly changed the way we operate mining equipment.”
AI-powered remote monitoring
Equipment monitoring in the mining industry is a high-stakes game: it’s time-consuming, and small failures can lead to operational downtime or even major accidents if overlooked. Chile’s Fukay Data has piloted a new technology to provide early warning diagnostics through AI monitoring.
The vitech system uses wireless sensors installed in mobile equipment components, which can be installed on all moving equipment in a mine from shovels, CAEX trucks, drillers and support equipment. Data from these sensors is wirelessly sent to the cloud before being downloaded and analysed by the software.
According to Fukay Data, the solution will make equipment monitoring faster, safer and less expensive, as technicians will no longer have to approach large-tonnage equipment to perform monitoring checks.
While the system is still in its pilot stage, it has already gained national attention in Chile, with Fukay Data winning the Impact Mining 2022 contest and a $31,000 (CLP$25m) grant to bring the technology to market.
Winning the prize is a huge leap forward for the project, one which the Fukay Data team are approaching with great excitement. “The award has filled us with joy and has strengthened the team to continue with our dream,” says Cristián Gallardo, technical manager of operations at Atecma Ingenieros Consultores on behalf of Fukay Data.
“It took three years to develop the solution and now we are in the important stage of the climax, so we feel that this award takes us to the future.”