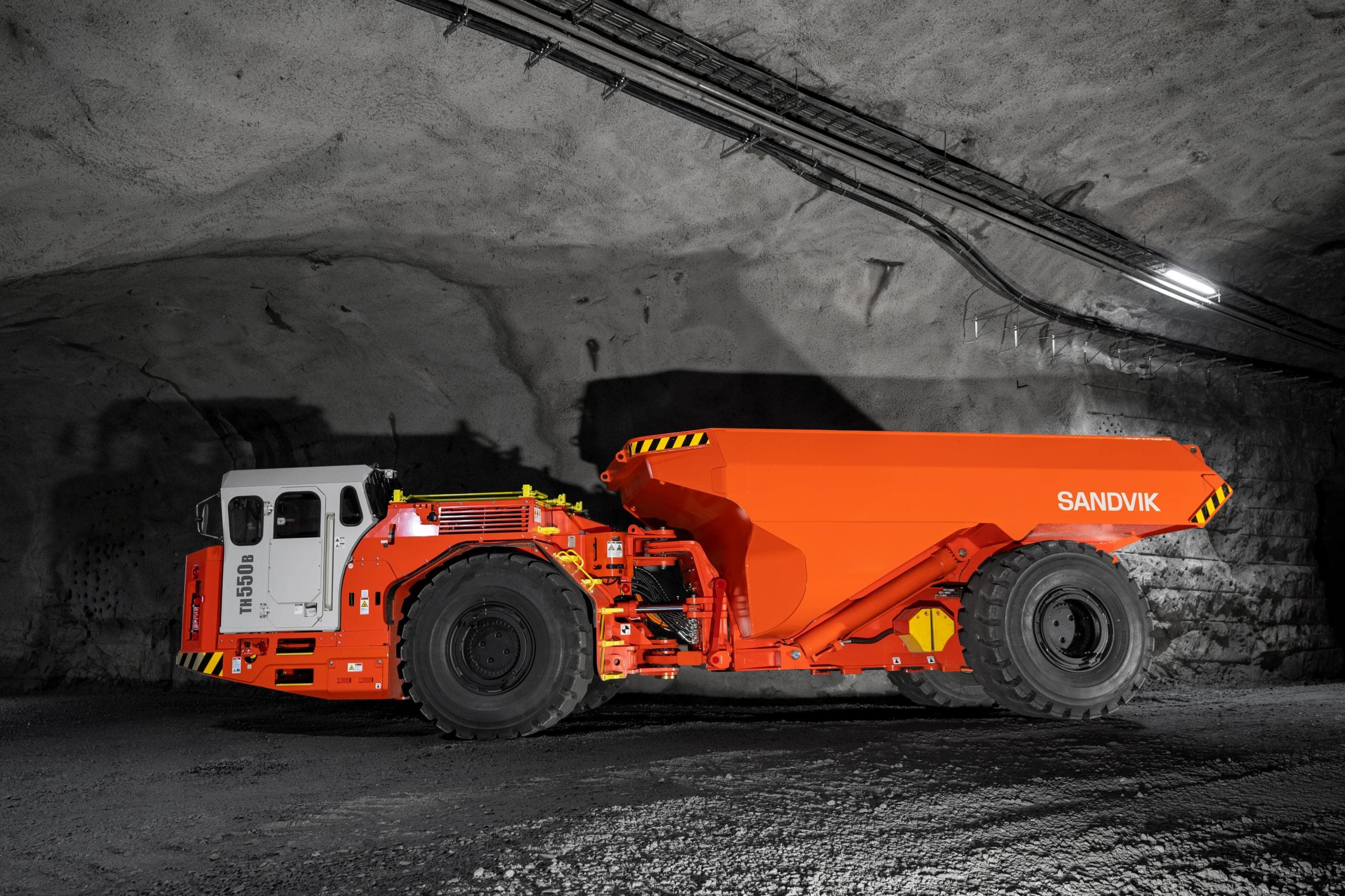
Headquartered in Stockholm, the reach of the Sandvik Group seems almost limitless. With a history dating back more than a century and a half, operations around the world, an estimated 44,000 employees and interests in fields as varied as mining and processing to manufacturing and specialist materials, the global powerhouse in high-tech engineering prides itself on innovation, collaboration and sustainability.
One of its most recent acquisitions best demonstrates its diversity; in early August it announced the purchase of Switzerland-based Sphinx Tools and its subsidiary P. Rieger Werkzeugfabrik AG. The deal saw Sandvik establish a foothold in the automotive, aerospace and medical markets, securing expertise in micro tools and surgical cutting tools. The news came just days after the company announced the purchase of US-based carbide, high-speed steel cut and roll forming tap supplier Balax. Both transactions fit into what the company calls its “shift to growth strategy”.
With this growth strategy in mind, there appears to never be a quiet time for the company’s mining and rock technology division, with corporate acquisitions and technological innovation commonplace for the company. Yet it remains to be seen how effectively these innovative and collaborative projects can be for the company, and the mining sector as a whole.
Electric vehicles
One of Sandvik’s best-known investments is into the field of electric mining vehicles, and the firm has not slowed down on this end. A fleet of 20 battery electric vehicles (BEVs) are headed to what is said to be the world’s first carbon-neutral copper development project at McIlvenna Bay in Canada’s Saskatchewan province. The company’s trucks, loaders and drills will support work at the clean hydroelectric powered facility, becoming Sandvik’s largest single fleet to date.
Speaking of the news, the company’s vice president of strategy and commercial at its battery and hybrid electric vehicles arm, Jakob Rutqvist, said: “BEVs have enormous potential to reduce a mining operation’s carbon footprint, and Canada continues to be the epicentre for mining electrification and a blueprint for what to expect in other major mining regions very soon.”
Foran Mining, which operates the underground copper-zinc project, will take delivery of seven Sandvik LH518B loaders, six Sandvik TH550B trucks, four Sandvik DD422iE jumbos, two Sandvik DL422iE longhole drills and one Sandvik DS412iE mechanical bolter between 2023 and 2025. Foran believes that by utilising battery–electric equipment with semi- and fully-autonomous capabilities, such as Sandvik’s, they will achieve carbon neutral targets and provide a safer working environment, part of its “Net Positive Business” programme.
How well do you really know your competitors?
Access the most comprehensive Company Profiles on the market, powered by GlobalData. Save hours of research. Gain competitive edge.
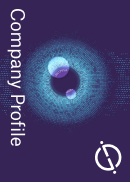
Thank you!
Your download email will arrive shortly
Not ready to buy yet? Download a free sample
We are confident about the unique quality of our Company Profiles. However, we want you to make the most beneficial decision for your business, so we offer a free sample that you can download by submitting the below form
By GlobalDataProjects such as these also demonstrate how many of the obstacles to widespread technological innovation can be overcome; Sandvik has partnered with a local firm with expertise in the region, and delivered a large enough fleet of BEVs that the vehicles are not some underrepresented oddity that require particular care and maintenance. In this manner, Sandvik’s steady expansion of its BEV fleet come prove to be something of a blueprint for other companies to follow.
App development
Any mining professional that has faced the challenge of having to determine the reason for failure will know how testing it can be. Sandvik is hoping to eliminate that, as much as possible, with its “My Rock Tools Analyze”, a new mobile app that aims to put support in the palm of customers’ hands.
Sandvik says the app is designed to help customers improve the performance of their rock tools, by removing the time-consuming, and potentially costly, human requirements for assessing and replacing tools. When in difficulty, users can log in, provide some key product information, take a few photos of their worn out tool and send it to Sandvik for analysis and feedback, a process that could provide tangible and immediately-effective support for miners at work.
A second app will help engineers in even the most remote of locations, providing access to a wealth of data and technical information about Sandvik’s products and the potential technical issues they might face. It draws together knowledge from across the business, making it accessible though searches, allowing users to look at product schematicsand watch tutorial videos.
It is currently undergoing a pilot roll-out, being used by 400 Sandvik technicians who are trailing it; it’s hoped that by the end of the year it will be available across the business, as a standard part of the service delivery it says.
However, as is the case with many automated or app-based processes, it is unclear if this process will be an adequate replacement for an on-site human expert in terms of the quality of assessment of tools and recommendations made for challenges. Indeed, considering the vast range of mines where Sandvik machinery operates, it could take some time before each mining tool and process is effectively covered by the apps’ databases.
Deswik acquisition
Sandvik has completed the acquisition of what it called the “leading and fastest growing major provider of mine planning software,” Deswik. The software, services and training provider for the mining industry will be incorporated into a new Digital Mining Technologies division at Sandvik, although it will remain a standalone enterprise.
Announcing the deal, Sandvik said: “Deswik’s evolution over the past 13 years has been filled with many significant milestones, and joining Sandvik is another important and exciting milestone in our history.” Sandvik had previously said that by acquiring Deswik, it would gain a top-tier supplier of integrated software platforms that support digitalisation throughout mine planning stages, with more than 10,000 current licenses, a range of licences that could stand Sandvik in good stead for future digitisation efforts.
Stefan Widing, Sandvik president and CEO, added: “Mine planning and operations management is a key growth opportunity, and this complementary acquisition and our new Digital Mining Technologies Division will strengthen our digital offering and enable us to provide customers a more comprehensive suite of technologies.”
Deswik brings considerable knowledge to Sandvik’s stable, and much of its technical knowledge will be used to improve the ‘upstream’ aspects of Sandvik’s supply chains. Sandvik has also enthused about opportunities for ‘end-to-end optimisation’ solutions, highlighting the company’s commitment to improving efficiency and operational effectiveness at all levels of its supply chains, not just in the mining processes themselves.
Sandvik named electrification at the mine planning stage, and the use of 3D design software to aid in mine construction, as examples of what Deswik could bring to the company. While these are exciting benefits, they are changes to the early, more theoretical stages of the mining process, and it remains to be seen if these commitments to modernising planning yield benefits across Sandvik’s much larger and more diverse supply chain.
3D manufacturing
Sandvik collaborated with Swedish multinational metals, mining and smelting company, Boliden, on what it called a “small-scale trial of 3D manufactured parts”.
The trial involved a set of specially redesigned components being digitally printed at a Sandvik facility in Italy, with the parts’ performance then being monitored on machines in Boliden’s underground mine worksites in Sweden and later Ireland, testing the theory that 3D metal parts could perform as well – or even better – than traditionally manufactured ones.
Speaking of the trial, Boliden’s head of supply management Ronne Hamerslag said this type of process, additive manufacturing, has a lot of potential, both in reducing the carbon footprint within the supply chain, through reduced or eliminated need for transport and storage of parts and also shorter delivery times. “This trial will give us a deeper understanding on how we can move forward and develop our business in a competitive way,” he added. “If you ask me, it’s the most exciting thing that’s happening in the supply chain.”
Sandvik’s Erik Lundén, president of parts and services, echoed those thoughts, adding: “Mining equipment can last up to 25 years – and needs to be supported throughout that time – even in the most remote of locations. We have many different stock keeping units, and from an inventory point of view we can’t tie up the capital that keeping all these parts in stock would entail.”
Of course, trials at a few individual mine sites are one thing, but replacing industrial parts on a large scale is something else entirely. While it is possible that 3D printing technology will scale across the world’s industries, this has not happened yet, and it may be some time before the world’s mines are stocked with 3D-printed parts.