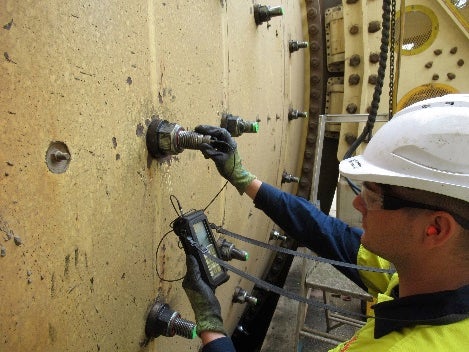
Boltstress Ultrasonics has been providing bolting solutions for over 30 years to the mining, refining, hydrocarbon, power generation, marine, motor vehicle, construction and fairground industries.
The foundation of its knowledge base has been built by measuring the actual bolt tension (not torque) achieved by any tightening method. The two key factors are ultrasonic bolt tension measurement, and joint analysis and management.
In the mining industry the process of re-torquing after a mill re-line is very common. It has been a necessity to re-torque bolts to reduce the number of failures, but it doesn’t need to be that way.
The top four root causes of failures are low pre-load, pre-load “scatter” inconsistent service processes, and high relaxation. Our solution is to measure and adjust every bolt to precisely the required bolt pre-load. Because our people do this so often, they are quick enough not to slow down the process. In most cases we actually reduce the reline durations.
Solution process
Prior to the re-line start, Boltstress calculates allowable tension for the bolts, determines allowable stresses for mating parts, sets up ultrasonic data files, and measures bolt loose reference lengths.
During the re-line, it allows the re-line crew to tighten one set per row of bolts, measures residual tension, calculates average tension, reviews and adjusts tooling pressure settings, re-tests on subsequent rows, and measures and adjusts all bolts to achieve the highest allowable pre-load and accuracy.
This process eliminates failure, reduces shutdown durations and creates a safer more efficient workplace.
Another point to consider is tooling, which is often bought to cover a variety of applications. There is a quicker and more accurate option if specifically engineered tools are used. We have a design team that provides lighter, safer and higher strength tooling.
Biggest contributor to failure is joint design
One of these common design failures is short clamp-length-to-diameter ratios. A 10° angle of turn is virtually impossible to see when tightening but affects bolt tension significantly.
Typically, a bolt 500mm clamp length will be stretched over 1.25mm, whereas as 150mm clamp length only requires 0.45mm. 10° equates to 0.125mm elongation, which is a 30% error on the short bolt but only 10% on the longer version. Moreover, loss of elongation due to relaxation is likely to be 0.4mm on any fishtail arrangement, or 32% on the longer bolt, but 90% on the shorter version. Consequently, shorter bolts often fatigue fail due to pre-load that is too low.
About Boltstress
We have 14 years of specifically working on Mill Liner bolts and can both eliminate failures and remove the re-torque process. In most cases the return on investment for our customers has a ratio greater than 10:1.