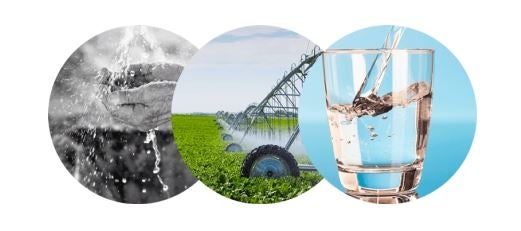
Quantum Filtration Medium manufactures an advanced oxidation catalytic filtration media called DMI65®, specifically tailored to oxidise and remove iron and manganese in solution. DMI65® also removes arsenic, aluminium, and other heavy metals. Additionally, DMI65® successfully treats turbidity, as well as hydrogen sulphide under certain conditions.
The catalytic surface of DMI65® contains manganese oxide, which facilitates covalent bonding of manganese and oxygen atoms from water. Its extremely powerful catalytic properties allow soluble iron and manganese to be removed, without the need for periodic media regeneration (e.g. with potassium permanganate). DMI65® is revolutionary due to its proprietary infusion technology that penetrates the microporous substrate of the matrix material, allowing for greater catalytic surface area with a tight particle size distribution.
Advanced filtration solutions for mining applications
The unique microporous structure of DMI65® removes dissolved iron and manganese to levels as low as 0.001 ppm or even to non-detectable levels. DMI65® has low levels of fines, good tolerance to a wide pH operating range and a catalytic surface that isn’t consumed or diminished when operated in accordance with vendor guidelines. DMI65® protects and pre-treats other water treatment systems (e.g. Reverse Osmosis) from iron and manganese biofouling, allowing longer filter run times, with the benefit of reduced oxidant demand. DMI65® has an operating life of 15+ years or more depending on the raw water quality, treatment application and user compliance to vendor operating guidelines.
The processes that take place in a filtration media bed of DMI65® involve reduction/oxidation (redox). Redox reactions involve a transfer of electrons between species. Reduction is the gain of electrons or a decrease in the oxidation state of a molecule, atom, or ion. Oxidation is the loss of electrons or an increase in the oxidation state of a molecule, atom, or ion. Redox reactions occur simultaneously, as there cannot be a reduction reaction without an oxidisation reaction.
Applications and advantages of DMI65®
DMI65® has been used prominently for many years in water and wastewater treatment facilities across the world, including: US Steel’s Big River Steel plant in Arkansas, USA; Chillagoe Arsenic Filtration Plant in Queensland, Australia; Pfizer Global Supply API/DP in Michigan, USA; George Municipal Water Works in Western Cape Province, South Africa; Kuala Langat Power Plant in Selangor, Malaysia; Fortescue Metals Group’s Cloud Break iron ore mine in the Pilbara, Western Australia; Southport Power Plant in North Carolina, USA; and the Southern Peru Copper Corporation’s Toquepala copper mine in Tacna, Peru.
Removal of iron and manganese
The presence of iron and manganese in water results in significant maintenance issues, loss of production and potentially system failure. DMI65® efficiently removes dissolved iron and manganese to concentrations as low as 0.001mg/L, well below regulatory MCL’s.
Removal of arsenic
DMI65® is a manganese dioxide (MnO2) infused silica sand based granular media, whose surface acts as an excellent oxidant and is effective in removing both arsenite and arsenate, as well as iron/arsenic complexes and precipitants to as low as 0.001mg/L.
Reduced costs
The total cost of DMI65® water filtration systems is significantly less than alternative solutions. This benefit is possible because the use of DMI65® provides advantages in treatment plant design, reducing capital expenditure and lowering operational expenditure on chemicals, power and backwash wastewater recovery.
High flow rates
The infusion technology of DMI65® promotes the highest oxidation rate of any catalytic water filtration media. This permits a significantly higher water flow rate to achieve the same level of iron and manganese removal. DMI65® can operate at linear filtration velocities up to twice that of conventional media, with a corresponding reduction in capital equipment costs.
High load capacity
DMI65® has a high iron and manganese load capacity, which can extend the duration of filter runs and the time between backwashing, thereby reducing downtime, operating expenses, and wastewater.
Regeneration not required
DMI65® operates with a continuous injection of sodium hypochlorite at low residual levels between 0.1-0.3mg/L, eliminating the need for media regeneration (e.g. with potassium permanganate).
Wide operating environment
Stable and satisfactory performance at pH 5.8 to 8.6 and a maximum operating temperature of 113° F (45°C) reduces the need for investment to alter the operating environment.
Long life
DMI65® is not consumed in the catalytic process, giving it an expected operating life of up to 15 years or more, depending on water quality, treatment application and user compliance to vendor operating guidelines. The media does not decay when doing its catalytic work. Over its long working life, DMI65® can experience attrition through mechanical abrasion during backwashing. The incremental loss of media from this impact is in the range of 1%-5% per annum.
DMI65® certification
- Tested and Certified Under Industry Standards: NSF/ANSI 61 by the Water Quality Association of USA Gold Seal Program covering safety and health effects for drinking water components.
- Compliant – Drinking Water Inspectorate safe to use according to: Reg. 31(4)(a) of water supply (Water Quality) regulations 2010 for UK, England, and Wales.