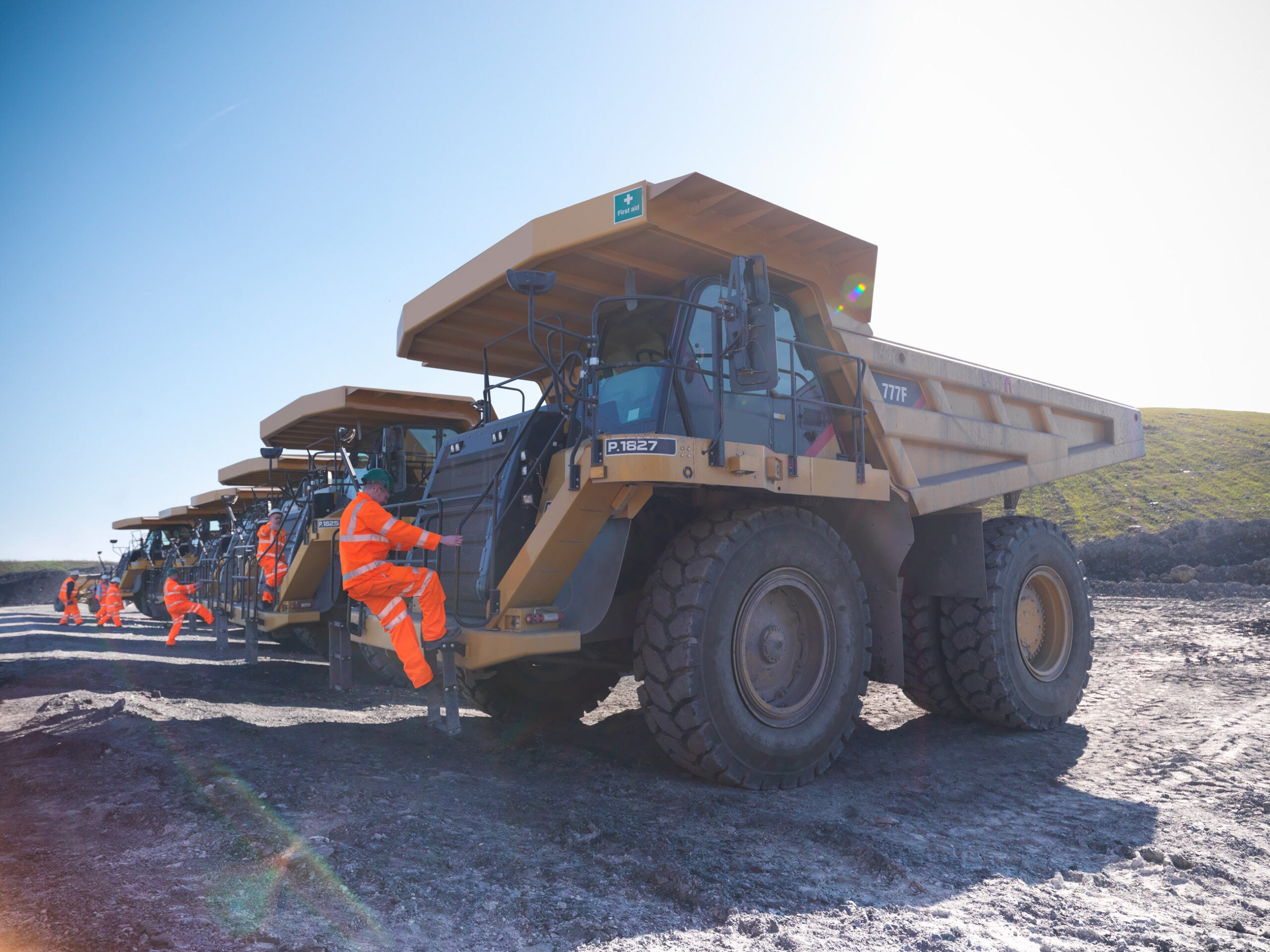
An indisputable potential advantage of autonomous vehicles is that they could provide increased safety, both on the road and near mining sites. Vehicle software is likely to make fewer errors in comparison to humans, meaning automation could decrease the number of casualties in mining operations.
After Fortescue completed its leading autonomous haulage project in October 2020, one of the largest fleet conversions to autonomous haulage in the industry, the company is ramping up its futuristic mobility plans with four recently rolled out, modified Ford Ranger vehicles.
How well do you really know your competitors?
Access the most comprehensive Company Profiles on the market, powered by GlobalData. Save hours of research. Gain competitive edge.
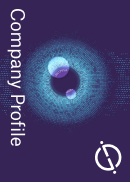
Thank you!
Your download email will arrive shortly
Not ready to buy yet? Download a free sample
We are confident about the unique quality of our Company Profiles. However, we want you to make the most beneficial decision for your business, so we offer a free sample that you can download by submitting the below form
By GlobalDataWhile last years’ autonomous haulage project expanded Fortescue’s haulage fleet to 183 trucks, operating at Fortescue’s Solomon and Chichester Hubs in the Pilbara region of Western Australia, the new venture is bringing extra value to the mining industry. The vehicles have now been retrofitted with on-board vehicle automation systems to reap more benefits.
Fortescue revealed that its technology and autonomy team had, in collaboration with Ford Australia, retrofitted the four Ford Rangers with an on-board vehicle automation system to set up driverless equipment transfer service at the site.
Fortescue’ Ford Rangers with on-board vehicle automation systems
The autonomous retrofits have been designed to find a transport solution for the Christmas Creek mobile maintenance team, cut time, and increase safety. Autonomous light vehicles (ALVs) remove the need for fitters to make around 12,000 28km round trips annually.
Fortescue was the first mover on autonomous haulage and became the first company in the world to deploy CAT autonomous haulage on a commercial scale.
The Ford Rangers were retrofitted with the on-board vehicle automation system, developed by Fortescue’s technology and autonomy team. The system features an integrated LiDAR/radar perception system that facilitates obstacle detection and dynamic obstacle avoidance; a comprehensive independent safety management and fail-safe braking system; and extensive built-in system monitoring and fault response capability.
The ALVs have been created to redefine the transportation at Fortescue’s operations by eliminating the need for workers to manually transport equipment, thus allowing them to focus on maintenance responsibilities, increased productivity, flexibility of work, and safe operation of assets.
Inside the autonomous light vehicles and Fortescue’s community efforts
While the ALVs have a dedicated road for the transport service, Fortescue CEO Elizabeth Gaines makes clear that they also have a range of additional safety mechanisms in place, including “collision avoidance capability, which uses both on-board sensors and logic procedures” in order to prevent incidents.
To prove their safety, Fortescue has trucks operating across its mining operations in the Pilbara, which have safely travelled more than 60 million kilometres to date.
Gaines explains: “To put this in context, our autonomous fleet has travelled a distance equivalent to 78 trips to the moon and back, without a driver at the wheel.”
As part of their collaboration, Ford Australia provided assistance in customising the vehicles to Fortescue’s specifications for the equipment transfer service. Fortescue and Ford said that they continue to work together to further improve capability in this area, focusing on the reduction of cost and increasing reliability.
In recent years, Fortescue has not only worked alongside like-minded companies, but has also looked to create community engagement and back up traditional owners of the land where the company’s Iron Bridge Magnetite project is located. For this reason, in January 2021, Fortescue awarded over A$13m in new contracts to the Aboriginal businesses Jukawalyi Resources and Yulu Joint Venture.
The future sustainability and ongoing success of Jukawalyi will be further supported, with Fortescue acting as a guarantor for the purchase of the vehicles, through Fortescue’s guaranteed leasing facility with the Australia and New Zealand Banking Group.
Hopes for the future
The project not only bears significance for major mining operations, but it also provides opportunities for development of skills, allowing team members to advance their in-house automation capability.
“Since the outset, Fortescue has been at the forefront of innovation in the mining industry, underpinned by our value of generating ideas,” Gaines says. “It is this focus on technology and innovation that has driven our industry-leading operational performance and cost position.”
The CEO also admits that the ALV project gives a significant chance of automation capability to build on its existing autonomous haulage system programme, which has demonstrated “productivity and efficiency improvements for the business”.
Looking ahead, Fortescue hopes that the successful deployment of the ALVs at Christmas Creeks will allow it to implement similar solutions at other operational sites. If proven successful, this trial could provide the company with an opportunity to implement a similar system at its other operational sites with an eye to improving safety, trust, and efficiency.
Gaines concludes that with the flexibility to introduce similar systems into other mobile assets in various locations, this project is fundamental to “the future of mobile equipment automation projects”.